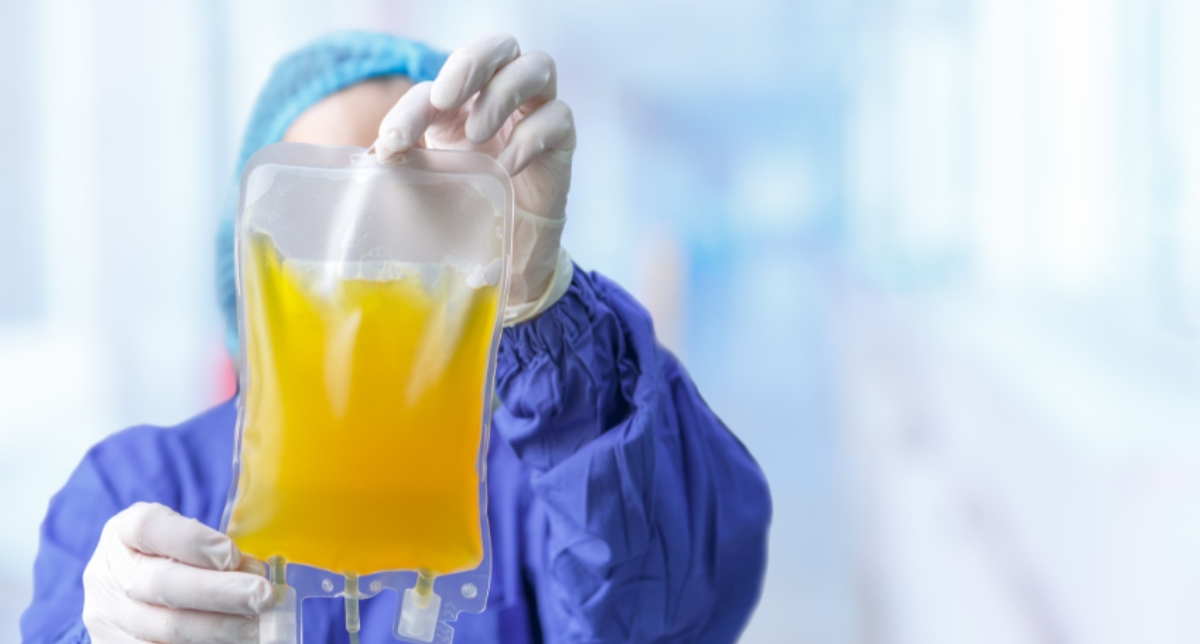
Pharmaceutical industry : opt for single-use filtering devices
The biopharmaceutical industry is increasingly using disposable single-use systems for the development and manufacture of a wide range of vaccines, therapeutic proteins and monoclonal antibodies (Mab's). What devices are available on the market ? What advantages do they offer ? And for which applications ? Techni Filtration takes stock.
Innovative, easy-to-install systems
Biopharmaceutical processes are complex and involve numerous steps, including filtration. In these industries, constraints in terms of purity, quality and compliance with standards are very high. In this demanding context, single-use systems, or SUS (single use systems) offer multiple advantages : reduced capital expenditure, shorter changeover times on production lines. They also bring flexibility to processes.
In processing industries (pharmaceutical products, but also agroalimentaire) requiring frequent and regular cleaning of equipment, SUS eliminates the need for time-consuming and costly clean-in-place (CIP) and sterilization-in-place (SIP) procedures.
The validation steps required when using reusable stainless steel systems also become obsolete when using SUS.
In research and R&D, SUS enable researchers and process engineers to work with different molecules - antibodies, proteins, vaccines, etc. - in the same facility. A definite advantage in the transition from laboratory to market for new drugs.
Ready-to-use, economical and flexible, single-use systems avoid the purchasing, maintenance and cleaning costs inherent in stainless steel filter housings, and dispense with CIP/SIP procedures.
Controlling extractables
Like any device in contact with a biopharmaceutical product, SUS can potentially release compounds into the latter, or interact chemically with it, altering its purity, composition and potentially its efficacy, or even making it unsuitable for marketing. Controlling the nature, quantity and development of extractable substances from SUS, made up of polymers, is therefore a major concern.
It is therefore up to the manufacturer who uses them to quantify these elements and their subsequent impact on drug purity. To achieve this, it is essential that SUS suppliers provide detailed information on extractables, useful for leaching studies.
Using gas chromatography-mass spectrometry (GCMS) or liquid chromatography-mass spectrometry (LCMS) analyses, for example, the supplier can accurately characterize the various SUS components for volatile, semi-volatile and non-volatile extractables, with several extraction media and under different time and temperature conditions.
SUS devices in practice : bags, filters and sampling systems
SUS are therefore designed to meet a wide range of requirements and needs : microbial retention, sterility, endotoxin filtration, biosafety... Existing devices are also designed to operate over a wide range of applications in terms of flow rate, burst strength, temperature, pressure, pressure drop...
In practice, disposable single-use devices are highly varied in nature. They may be sterile bags, sampling systems, filtering devices (filter capsules in particular), tubes, connectors, etc.
2D & 3D sterile bags are used for the storage and transfer of sterile media, intermediates, sterile buffers with a wide pH range, sterile drug substances and formulations.
The storage and transfer of these fluids during and between process steps, and between different process zones, is particularly critical. Disposable, pre-sterilized storage and transfer systems meet regulatory requirements in this field, while preserving the nature, strength, quality and purity of the fluids.
Sterile pouches are made from a multi-layer polyethylene film that is highly inert to the chemicals and solvents used in the biopharmaceutical industry. They offer an excellent barrier to oxygen, CO2 and humidity.
Single-use, γ-irradiated aseptic sampling systems are used for aseptic fluid sampling at various stages of pharmaceutical and biopharmaceutical processing. They can cover the following needs :
sterile bulk and sterile transfers, vaccine formulation at various stages of maturation, fermentation cycles, cell culture from bioreactors.
Multiple tubing options in thermoplastic elastomers (TPE) as well as platinum-hardened silicones are available, in a wide range of internal and external diameters to suit all needs.
Last but not least, filters, including filter capsules, are particularly suitable for pre-filtration, microbial load reduction and sterilizing filtration applications.
Focus on single-use sterilizing capsules
Filter capsules, also known as monobloc filters, are available in a range of formats and media types, in sterilized or non-sterilized gamma versions. Ready to use and particularly well suited to development, pilot or batch filtration, they offer ease of use appreciated by operators.
They are used for pre-filtration, microbial load reduction, sterilizing filtration and final filtration stages, from sample preparation to larger batch packaging. The filtration unit is enclosed in a filter capsule, limiting set-up or maintenance operations and operator exposure. They can be ordered pre-sterilized for immediate use in an aseptic environment.
Disposable filter capsules use media made of PES, PP, hydrophilic or hydrophobic PVDF, PTFE, glass microfiber, nylon or filled nylon. Suitable for gas and liquid filtration, they are available in different pore sizes, lengths and connection types, and cover a filtration threshold range from 0.1 to 20 μm. A wide range of filtration surfaces is available, from small 5 cm² capsules with very low retention volumes to 18,000 cm² filters for large-scale production.
For all filter capsules, inlet/outlet connections are either standard or customizable.
Capsules with hydrophilic PES or PVDF membranes are particularly recommended for sample preparation, clarification and microfiltration of cell culture media, both upstream and downstream. Whether for sterilizing filtration of pH adjusters, growth regulators, antibiotics or vaccines, these sterilizing membranes are compatible with ethylene oxide, γ-radiation and autoclave sterilization methods.
Hydrophobic membrane filters are used for pressurized gas filtration or tank venting. Their PTFE or polyvinylidene fluoride (PVDF) membrane reliably removes contaminants and micro-organisms in sterilization applications.
Filter capsules specially designed for higher flow rates are also available. With a low protein adsorption rate, PES and PVDF media offer high chemical compatibility with extremely low extractables, both on a pilot scale and for larger production batches.
Filter capsules must be manufactured in a clean room (ISO class 7), under the control of a strict quality management system, to ensure total traceability and consistent production quality for the user. Each capsule must be accompanied by an individual certificate of conformity.