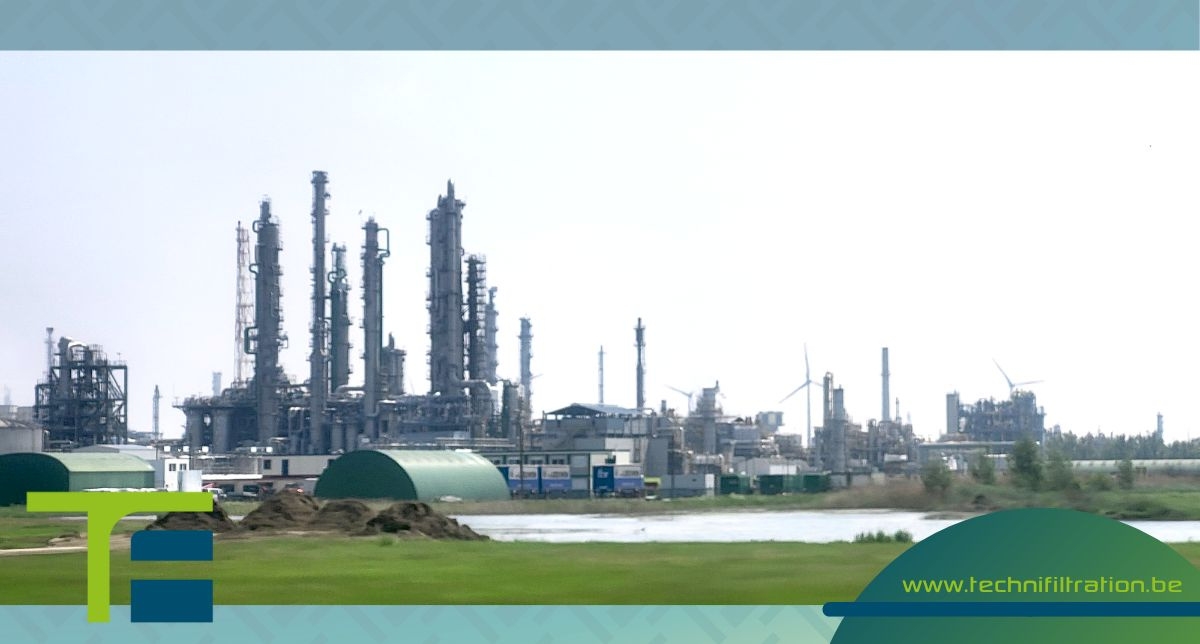
Petrochemie : hoogwaardige filtratie vereist !
De petrochemische industrie gebruikt zeer specifieke filters voor de behandeling van chemisch agressieve verbindingen, die vaak zeer viskeus zijn en tot hoge temperaturen verhit worden. Afhankelijk van de toepassing zijn de te filteren vloeistoffen zeer gevarieerd: oliën, brandstoffen, gassen maar ook water en oplosmiddelen. In olieraffinaderijen is de zuiverheid van de geproduceerde brandstof van cruciaal belang. In de polymeerindustrie worden filters gebruikt zodra de grondstoffen in de tussenreactor worden gebracht, en vervolgens in elk stadium van de synthese: polymerisator, menger, extruder, enz. De te filteren stoffen hebben zeer uiteenlopende reologieën (water, oplosmiddel, gesmolten polymeren) en chemische samenstellingen (polypropyleen, polyester, polyethyleen, enz.). Om de confrontatie met deze filtratie-uitdagingen aan te gaan, bieden metalen filters grote voordelen.
In een raffinaderij wordt ruwe olie in drie fasen omgezet in eindproducten: scheiding, conversie en opwaardering.
De eerste stap is het scheiden van de moleculen door destillatie volgens hun molecuulgewicht. Hiertoe wordt de olie verhit tot temperaturen van ongeveer 350-400°C om in een destillatietoren te verdampen. De dampen van de ruwe olie stijgen in de toren terwijl de zwaardere moleculen, ook wel zware residuen genoemd, aan de basis blijven zonder te verdampen. Terwijl de dampen opstijgen, condenseren de moleculen in vloeistoffen, de een na de ander volgens hun grootte, op de "distillatieplaten" die over de hoogte van de toren zijn verspreid. Alleen de lichtste verbindingen bereiken de top van de toren, waar de temperatuur slechts ongeveer 150°C bedraagt, in gasvorm. Elk plateau komt overeen met een destillatiefractie, ook wel petroleum cut genoemd. Onderaan de toren bevinden zich de bitumen (de meest viskeuze koolwaterstoffen), bovenaan de gassen.
De producten van gemiddelde dichtheid zitten op hun beurt vaak gevangen in de zwaarste residuen. Deze worden daarom onderworpen aan een tweede distillatie om de tussenproducten (zware stookolie en gasolie) te extraheren. Na de scheidingsfasen, en om de zware producten terug te winnen, worden deze zware moleculen afgebroken tot lichtere moleculen. Dit omzettingsproces, uitgevoerd bij 500°C, wordt katalytisch kraken genoemd. Gemiddeld wordt 75% van de aldus omgezette zware producten omgezet in gas, benzine en diesel. Andere processen, zoals hydrokraken, kunnen dit resultaat verbeteren.
In een laatste fase, de zogenaamde opwaardering, kan het gehalte aan corrosieve of voor het milieu gevaarlijke moleculen, zoals zwavelverbindingen, aanzienlijk worden verminderd. De ontzwaveling van diesel geschiedt bij 370°C, onder hoge druk (60 bar) en in aanwezigheid van waterstof. Zo wordt de zwavel die in aardolieproducten aanwezig is in de vorm van waterstofsulfide (H₂S) geëxtraheerd. Paraffine, butaan en propaan worden gewassen met soda om de thiolen die ze bevatten te verwijderen.
Aan het einde van het raffinageproces heeft elke samenstelling van ruwe olie een specifiek gebruik:
benzine en diesel worden gebruikt voor automotoren, LPG (vloeibaar petroleumgas) wordt gebruikt als brandstof voor voertuigen die op gas rijden, butaan en propaan dekken de huishoudelijke behoeften, paraffine wordt gebruikt als brandstof in de luchtvaartindustrie, nafta wordt gebruikt als grondstof in de petrochemie, huisbrandolie wordt gebruikt als verwarmingsbrandstof, oliën worden gebruikt voor de vervaardiging van smeermiddelen, en tot slot wordt bitumen gebruikt voor de bekleding van wegen.
In raffinaderijen worden filters gebruikt in de hele productieketen: stroomopwaarts (filtratie op waterinjectiecircuits, bescherming van omgekeerde osmosemembranen, proceswater) maar ook stroomafwaarts (gasscheiding, aminevermindering, katalysatorbedden, enz.).
In de olie-industrie worden grote hoeveelheden water gebruikt om de druk op peil te houden en de productiviteit te verhogen. Daarom moet bijzondere aandacht besteed worden aan de kwaliteit ervan, of ze nu vers of zout is. Het water kan vol zitten met algen of plankton, slib en andere sedimenten die de prestaties van de installaties kunnen schaden.
Zodra de brandstoffen verkregen zijn, worden zij opgeslagen in grote tanks voordat ze via pijpleidingen of tanks worden gedistribueerd. Tijdens deze opslagfase raken ze belast met verontreinigende stoffen (roest, kleine deeltjes,..), die stroomopwaarts van de distributiepunten problemen kunnen veroorzaken. Zo kunnen ze de apparatuur van de eindverbruiker beschadigen en zelfs de kwaliteit van het eindproduct doen verminderen. Het is daarom van essentieel belang dat brandstoffen vóór levering gefilterd wordt en gehomogeniseerd om deze verontreinigingen en eventuele aanwezigheid van water te verwijderen. Dit wordt bereikt door het gebruik van metalen filters of, wat minder vaak voorkomt, polymeer mediafilters. Deze filterapparaten moeten vaak op maat ontworpen worden om te voldoen aan de grootte van de installatie waarin zij zullen geïnstalleerd worden.
Voorbeeld van een patroon van geweven Inconel® 600-vezels :
De polymeerindustrie verwerkt bepaalde verbindingen die voortkomen uit de raffinage van ruwe olie (met name nafta) tot kunststoffen met een hoge toegevoegde waarde: productie van PET (polyethyleentereftalaat) en PP (polypropyleen) vezels voor de vervaardiging van plastic flessen, verpakkingsfilms, technische thermoplastische materialen of röntgenfilms, enz. Deze kunststoffen worden verkregen door polymerisatie, een chemische reactie die het mogelijk maakt een repetitieve opeenvolging van kleine moleculen te creëren om grote moleculaire ketens, de polymeren, te vormen.
De processen voor de productie van polymeren uit aardoliederivaten omvatten verschillende filtratiestappen. Om vezels van hoge kwaliteit met weinig breuk en een hoog rendement te verkrijgen, moet de polymeermassa homogeen zijn, zonder gelvorming of hoge overconcentratie. Het gebruik van filters verbetert de eigenschappen van de geproduceerde polymeren. In de polymeerindustrie moeten filterpatronen gemaakt zijn van een materiaal dat bestand is tegen de drastische bedrijfsomstandigheden op de productielijn: hoge druk en temperatuur, corrosie, hoge viscositeit, enz. Metalen filtermedia worden gebruikt in de vorm van geplooide en cilindrische filters, kapselfilters of schijffilters. Deze filters worden geleverd met een verscheidenheid aan eindfittingen die geschikt zijn voor alle bestaande filterbehuizingen of tankconfiguraties.
Wilt u meer weten over de verschillende filtratieoplossingen in de petrochemische industrie, lees dan de volgende artikelen:
- Alles over kaarsen- en schijvenfilters voor kunststofverwerking
- Meer informatie over polypropyleenfiltratie
- Meer informatie over polyisobuteenfiltratie
Metalen filters worden veel gebruikt in raffinaderijen en fabrieken voor de productie van kunststoffen op basis van aardolie, omdat zij door hun eigenschappen kunnen voldoen aan de specifieke eisen van deze industrieën.
In raffinaderijen worden bijvoorbeeld geplooide filterpatronen gebruikt van metaalvezels die mbv sinteren zijn samengesteld. Ze hebben een uitstekend vuilvasthoudend vermogen en een hoge porositeit. Zij kunnen ter plaatse worden gereinigd zonder het filtratieproces langdurig te onderbreken.
Polypropyleenfilms kunnen geproduceerd worden met poedervormige metalen filtermedia van roestvrij staal of innovatieve legeringen op nikkelbasis zoals Hastelloy®, die bijzonder corrosiebestendig zijn. Met dit type media kunnen filterelementen vervaardigd worden die zorgen voor een doeltreffende dieptefiltratie met een lange levensduur.
Deze metaalfilters zijn verkrijgbaar in een reeks poriegroottes van enkele microns tot submicron structuren. De filtermedia zijn gegoten in cilindrische elementen of als geplooide patronen.
Zie voor meer informatie ons artikel over het gebruik van metaalfilters
Deskundig advies: Ongeacht de gebruikte technologie (vezel, doek of poeder) hebben alle metalen filters een uitstekende mechanische sterkte en zijn ze bestand tegen aantasting in kritische toepassingen. Ze kunnen op maat worden gemaakt om perfect in de bestaande installaties te passen. |
Hebt u vragen over metaalfilters in de petrochemie? Neem contact op met onze deskundigen voor advies. |
Wens je meer informatie na het lezen van dit artikel of ben je op zoek naar een luisterend oor voor uw probleem, advies op maat? Raadpleeg onze deskundigen via onze contactpagina om u te helpen de meest geschikte oplossing voor uw proces te vinden en te valideren.
Zin in meer?! Volg onze pagina want er volgen meer interessante artikels over filtratietechnieken, al +20jaar onze énige focus en specialiteit.
Dank voor uw aandacht en interesse! Blijf op de hoogte te blijven van de wetenschap rond filtertechnieken : LinkedIn/TechniFiltration